Silver mountain style
September 26, 2017
When I started mountain biking all spokes were silver. It’s not as common these days but I think we should bring this look back. This is a set I did last month — they look great.
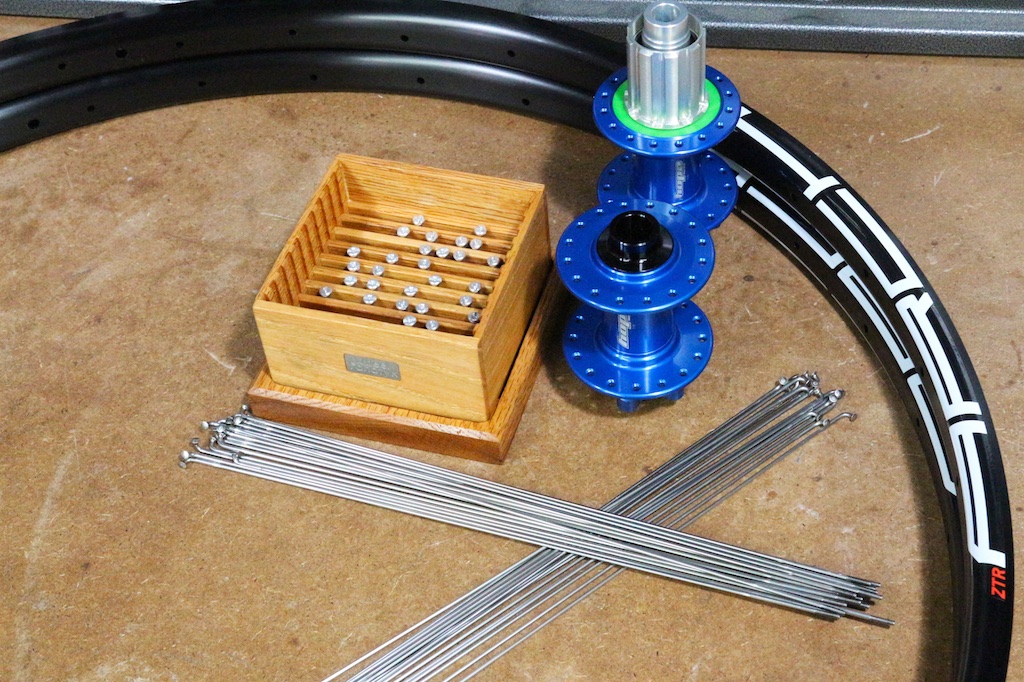
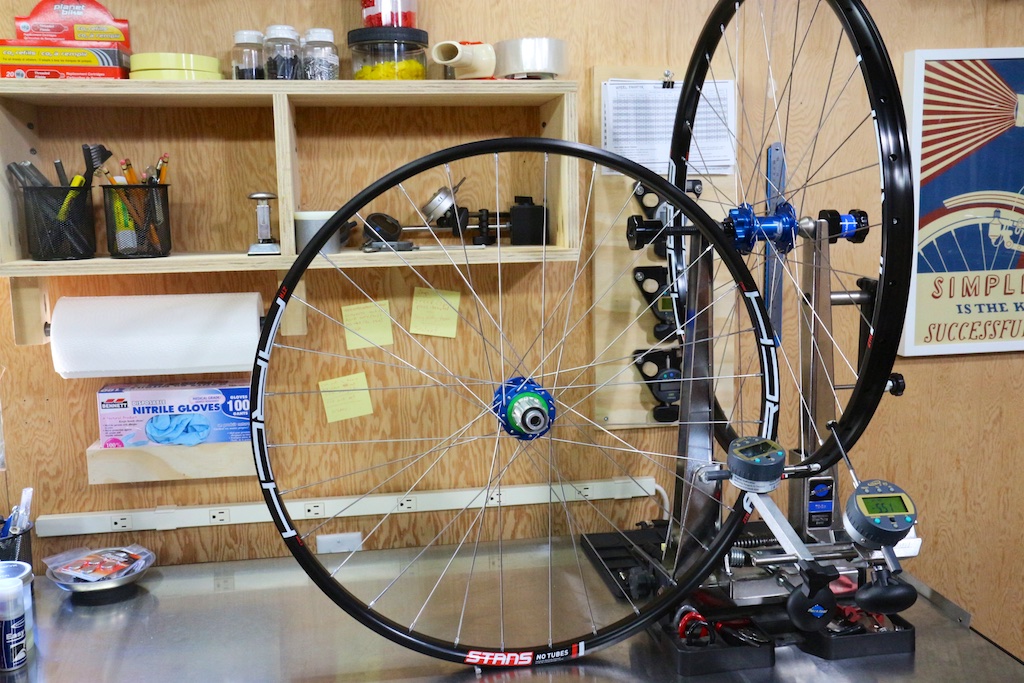
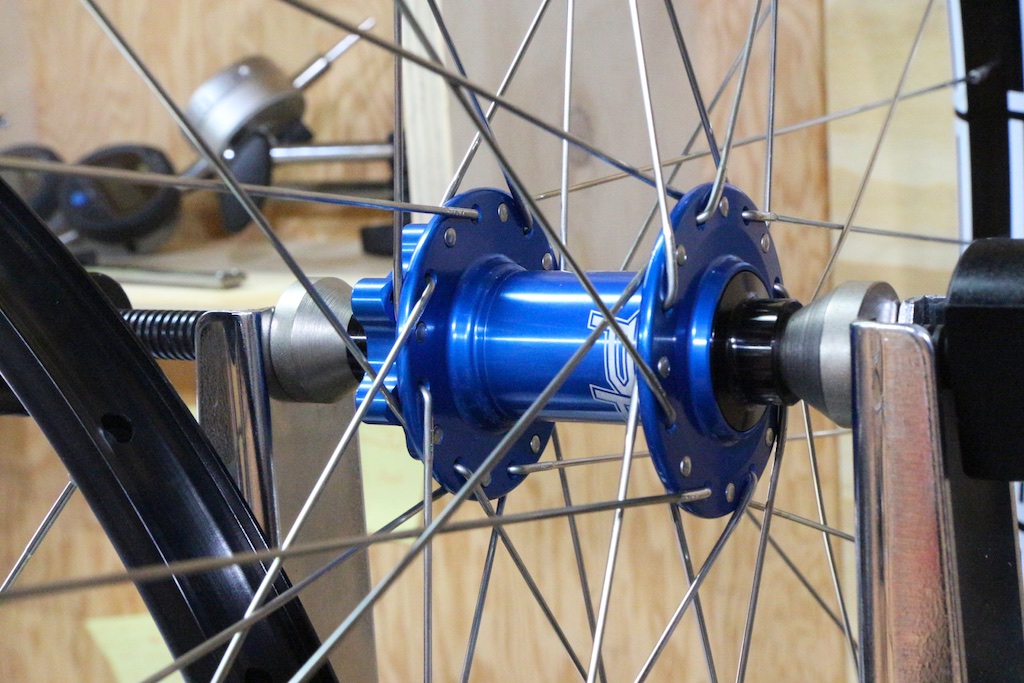
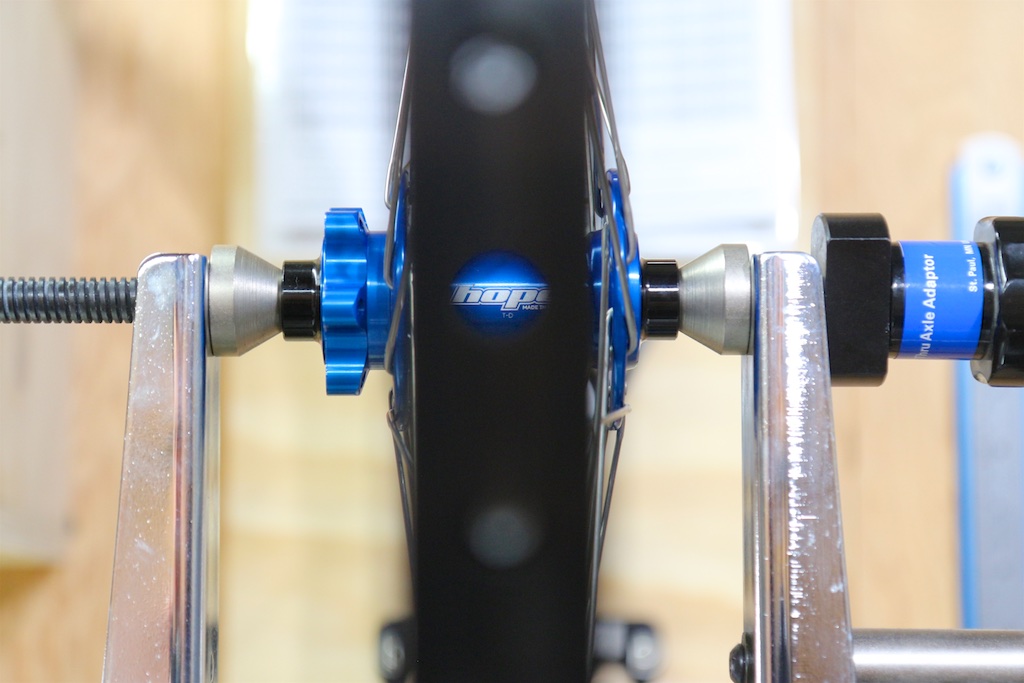
When I started mountain biking all spokes were silver. It’s not as common these days but I think we should bring this look back. This is a set I did last month — they look great.
This is a set of XC MTB wheels using DT Swiss 240S hubs and Light-Bicycle carbon rims. The rims are asymmetric, which allows for more balanced tension between sides of each wheel. The package is put together with Sapim D-Light spokes and Sapim aluminum nipples to keep weight low — only 1464 grams for the set. Tubeless-ready using Stan’s tape and valves. Very nice wheels.
Pros measure the effective rim diameter (ERD) of every rim.
My tools are DIY, which is inexpensive. Here’s how I make them: take two black 310mm Sapim Leader spokes and cut off the elbow leaving a 300mm rod. Use bolt cutters or a hacksaw to get close, then creep up on 300mm exactly using a file or a grinder. Screw a silver nipple to each rod using a bit of Loctite so they never move. For my process I make sure the spoke penetrates the nipple until it’s flush with the bottom of the screwdriver flats — spokes stretch a little under tension so they’ll end up in a good place. That’s it. If you’re precision-minded, you can ensure nipple geometry isn’t a factor by making a new set of measuring rods any time you build with a new variety of nipple.
Usage is straightforward. Insert your measuring spokes into opposing spoke holes, counting them to make sure you’re not off by one. Pull the spokes tightly across a ruler. To make the process easier and more accurate, try raising the ruler with a shim so the spokes leave the rim closer to 90°. Use a ruler with 0.5mm resolution (such as this one) or eyeball to the same. For most builds the spokes will overlap on the ruler, in which case you deduct the overlap length from 600mm. If the spokes don’t overlap, add the gap length to 600mm. Perform at least two measurements 90° apart and average the results to get ERD.
Note: you don’t need 300mm spokes to make a tool but it makes the addition/subtraction less error-prone. Use what you have but adjust the arithmetic factor to the sum of the length of your rods. If by some trick you end up with 300mm and 299mm rods, carry on using 599mm in your calculations instead of 600mm.
If you’re building with nipple washers, remember to increase spoke length to compensate. As an alternative, you can install nipple washers on your measuring spokes and build nipple washers right into your ERD. With asymmetric washers it’s helpful to give your measuring spokes a spin after pulling them taut just to make sure everything is seated properly. Overall this approach accounts for the end-to-end nipple/washer/rim fit and avoids errors from incorrect nominal measurements (a real thing).
Most spoke calculators will give you lengths to the tenth of a millimetre, which you’ll need to round to the nearest available length. Since measuring as above targets the bottom of the acceptable range, resist rounding down for low tension builds or on the low tension side of a wheel. In a future blog I’ll expand on the topic of rounding.
Sometimes newbies ask about cheap rims to try wheelbuilding, which isn’t the right way to think about starting. Rim quality sets the stage so inexpensive rims may serve to frustrate more than anything. If you’re apprehensive about wheelbuilding, and there isn’t any reason to be, stay away from ultralight rims and low spoke count rims. Stay away from ultralight spokes. Buy a quality rim with the attributes you want to ride and you’ll do fine.
This is another build using China-direct carbon rims. These are tubulars from Light-Bicycle, a brand featured on this blog a few times. They’re nice rims. The new infosheet from LB says special skills are required to build carbon rims but I can’t agree. If you’re smart enough to use a tensiometer, you can build carbon. I like nipple washers with carbon but otherwise my process is the same.
A recent build using economical carbon rims from Light-Bicycle. I selected Sapim D-Light spokes and aluminum nipples to save weight without compromising durability. Came out great!
White Industries T11 hubs mated to Stan’s Alpha 400 rims is a combination I’ve built (and ridden) in more than one incarnation. This set is put together with Sapim Laser spokes in the front and rear non-drive side, Sapim Race rounding out the rear. That puts total weight a hair over 1500 grams while remaining stiff enough for the rider. These wheels are setup tubeless with Stan’s tape and valves supporting Schwalbe Pro One tires in 700×28. A perfect combination top to bottom.
Thanks to Ric from Wheel Fanatyk for scanning a series of articles on wheels and wheelbuilding. They cover a lot of ground that will interest wheelbuilders new and old. Download in PDF.
It was a pleasure building these fancy WTB CI31 rims to DT Swiss 350 hubs. Normally I find myself building China-direct carbon rims but the brand name stuff is great too.
One challenge a wheelbuilder faces is managing spoke windup. Windup happens when friction between spoke and nipple causes the spoke to twist instead of tightening. This is bad because a twisted spoke is not in equilibrium and will eventually unwind. When twisted spokes unwind, wheels lose alignment. Windup worsens as spoke diameter decreases, which makes thin spokes like DT Revolutions more difficult (thicker spokes build more easily). The problem worsens as tension increases, which is a bigger issue in the 11-speed era because higher tensions are typically required.
There are a few strategies for dealing with spoke windup. The first and most fundamental is to make sure nipples receive ample lubrication. Sometimes adding more lubrication during a build helps. The second strategy is to detect spoke windup and compensate. Windup can be detected by feeling the spoke rotate in tandem with turns of the nipple (a flag can be fixed to the spoke to provide a visual cue). When you start experiencing spoke windup, it’s helpful to overturn the nipple and then back off. For example to achieve a quarter turn of the nipple, tighten the nipple a half turn then loosen by a quarter turn. Windup is released during the loosening step.
Before a wheel is declared complete it should be free of windup. Windup can be freed by flexing spokes in different ways. One way is to grab roughly parallel pairs of same-side spokes and pull them together. A more drastic method is to put the wheel on the ground, touch the ground with the hub and press down around the rim. You can often hear pinging noises as spokes unwind. A wheel is complete when these procedures do not change the wheel and other tolerances are met.